July 31, 2024 | Application NotesOil / Refinery
HTI Hydrocarbon Technology & Innovation, LLC
Pilot Plant Facility – Lawrenceville, NJ
Construction Costs: $400K
HTI’s mission is to offer world class catalytic solutions, technical consultation, engineering design and services for the traditional petroleum refining, coal conversion and renewables markets. HTI conducts research and development at its own Pilot Plant facility in Lawrenceville, New Jersey to support this mission and offers access to its technical resources to 3rd Party Clients on a service basis.
HTI is investing in new pilot plant capacities to expand its testing portfolio and has recently completed construction on a one of a kind 2-Stage hydroprocessing pilot unit with interstage stripping. This unit can operate in recycle and once-through modes using a variety of feedstocks. HTI’s target with this unit is to pilot traditional 2-Stage hydrocracking applications, as well as renewables and advanced recycling technologies.
Requirement
An intrinsically safe control system for monitoring temperature, flow, pressure and level in their process. NSI was contracted to design, build, integrate, install, and wire this system. The enclosure consisted of a purging system, IS isolators and 100 power controllers for electric heaters. The controllers communicate back to the Eurotherm T2750 control system in the control room. The use of an Eaton MTL 838 IS remote I/O system reduced the thermocouple installation by over 50%.
Services Provided
- Built & Wired Intrinsically Safe Enclosure with Purging & Isolators
- 120 PID Loops
- Custom Panel Creation
- Field Installation
- Configuration
- Custom Engineering Drawings
- Integration of Measurement & Process Control Instrumentation
- Trained Staff & Provided Back-End Support
- Network Set-Up
- Custom Touchscreen HMI Design with 200 Screens
- 3000 HMI Tags & 10,000 Project Tags
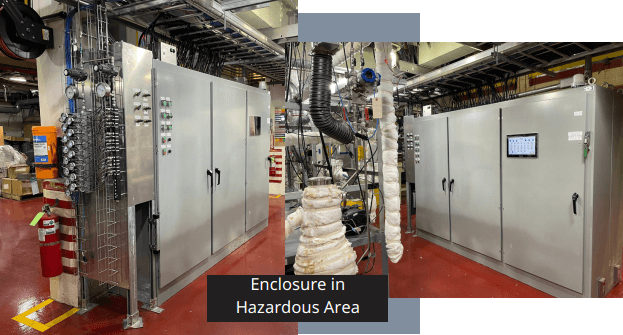
Products
- Eurotherm T2750 PAC Racks
- Epack SCR Power Controllers
- MTL 830C Temperature Multiplexor System
- MTL 5500 Series IS Isolators
- Custom Touchscreen HMIs
- Hirschmann Bobcat Managed Switches
Features
- Partial / Full Load Failure Detection for Electric Heaters
- Alarming (Modbus TCP Communications)
- Visualization in Hazardous Area Environment
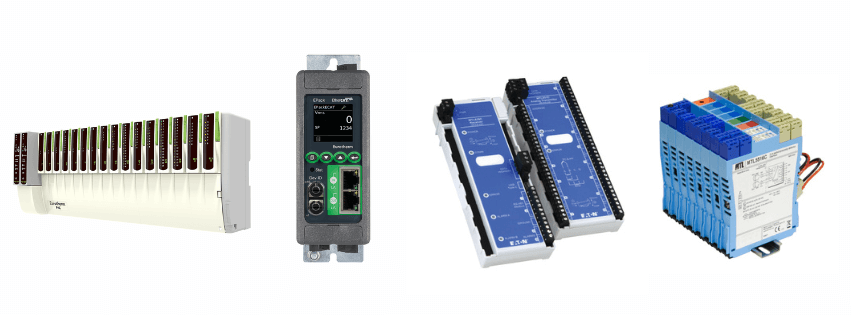
CONTACT US HERE FOR YOUR SOLUTION NEEDS