October 25, 2021 | Company News
You might know Dexter Vilar as one of the faces of Neal Systems! Dexter is our lead application engineer and has been a staple trainer for Neal Systems from the start. He has an electrical engineering degree from Penn State, and extensive application engineering and technical support background in instrumentation, controls, drives, and recorders. His specialties at NSI are:
- Draeger Gas Detection
- Eurotherm Controls and Data Acquisition
- Foxboro Temperature, Pressure, and Flow Meters
- Control Valves
- Intrinsic Safety Wiring Practices
- Explosion Proof Wiring Practices
Most recently, Dexter presented a course entitled Toxic and Combustible Gas Leak Detection in the Water Industry at the American Water Works Association’s 2021 New Jersey Section Annual Conference. If you are interested in this course or others in Dexter’s areas of expertise, please contact us directly to arrange having this presentation and more delivered to you and your facilities staff personally. This can be accomplished on-site at your facility; virtually; or at our recently expanded Newtown, PA facility, which features a 16-person Training Classroom and Instrument Wet Lab.
October 12, 2021 | Company News
Most of the parts that are heat-treated in America for use in planes, rockets, or space flight vehicles are treated in furnaces that adhere to a standard known as NADCAP (National Aerospace and Defense Contractors Accreditation Program). According to Peter Sherwin, one of the heat treat experts from Eurotherm, the goal of this standard is to ensure that we “reduce the variation in output from a heat treat furnace.” The standard, known as AMS (Aerospace Material Specifications) has a specific section that is geared toward the temperature measurement, control, and recording – AMS2750 (currently on revision F).
In this video of heat treat experts, a discussion about what the future holds for pyrometry specifications reveals some interesting tidbits about what we might see in AMS2750 Revision G, how the standards need to more dynamic, and how standards followed already in the pharmaceutical industry might make their way to aerospace.
NSI watches these changes carefully, as they significantly impact our digital solutions for measurement, control, and data acquisition that we provide to heat treaters looking to comply with regulatory standards for their furnaces.
September 8, 2021 | Company NewsProduct News
One of our engineers was recently asked “What is unique about Draeger Sensors?” by a chemical company evaluating the technologies from various gas detection companies. The engineer talked for about 30 minutes about all of the special capabilities and design features of the various Draeger sensor, and the company who had asked the question was blown away – they immediately decided to switch to using Draeger for all of their future gas detection needs. After that discussion, we recognized that perhaps all of our readers would benefit from the discussion as well!
Draeger scientists are constantly challenging, testing, and improving their 30+ electrochemical sensor types that they manufacture at their facility in Germany. While there are dozens of unique technology features in
each sensor, we typically focus on six unique ones that set Draeger e-chem sensors (pictured) apart from most other sensors on the market:
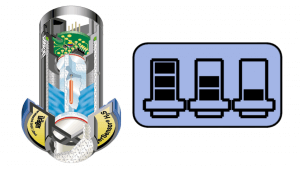
Built-in Memory Chip: Draeger has had this feature around for 20 years, but it still sets the sensor apart. The memory chip stores calibration data, gas exposure data, temperature exposure data, and other useful maintenance data. The key one is the calibration data – Draeger’s e-chem sensors arrive from the factory pre-calibrated, so that once they are plugged into a Draeger transmitter with the ability to read the chip, the sensor can start being used once it warms up!
Diffusion Hole for Pressure / Humidity: Many years ago, an industrial gas supplier tested Draeger sensors against a variety of other sensors in environmental chambers that could vary temperature, pressure and humidity. The Draeger sensor performed so much better than all of the other sensors (i.e. almost no drift) that they thought something was wrong with it! However, Draeger has designed their e-chem sensor with both an internal temperature sensor as well as a diffusion hole in the side of the sensor that allows it to quickly adjust for any gradual temperature / humidity / pressure changes that might occur. This is especially valuable when the sensors are mounted outside, or around inside areas that could see significant swings due to outside doors opening and closing nearby.
Circular Chemical Reaction and Large Electrolyte Reservoir: Draeger e-chem sensors typically last a LONG time, and don’t need calibrated all that often (we recommend typically every 6 months). We’ve had oxygen sensors last 10 years in some environments! A lot of this is related to the internal chemistry that often has a replenishing reaction (the two reactions replenish the reactants), as well as a very large reservoir of electrolyte. Most sensors last at least 3 years, and the days of calibrating once a week or once a month are largely erased when using a Draeger sensor.
Cross-Sensitive Gas Testing: What’s one of the biggest challenges with utilizing a gas detection system? Workers not trusting the system because of false alarms. But how do you know which gases might drive a sensor to give an inaccurate reading? While not specifically a technology design feature, the data sheet for each Draeger sensor provides extensive information about various gases that Draeger has specifically tested against the sensor to determine whether there are any cross sensitive gases for users to be aware of which can yield positive or negative readings.
Gas-Specific Filters: What happens if you need to measure a gas, but there are definitely cross-sensitive gases that are also present that will definitely cause significant reading errors? In many cases, Draeger has designed gas-specific filters that replace the standard dust filter. These filters absorb the cross-sensitive gas for a period of time (until they are full), and allow a normal measurement to occur!
Self-Diagnostic Capability: Ever had a gas detection sensor “fall asleep” and not provide any warning whatsoever? That can be a major concern for a safety system, and can drive maintenance teams to do far more sensor calibrations / bump tests / replacements than necessary. Draeger has designed in two levels of sensor diagnostics – a standard level for every sensor that detects key problems, and a higher level from an added chip that we’ll address in our next blog (the Draeger Sensor Diagnostic Dongle). The standard level will look at things like calibration speed of response, calibration sensor gain level, sensor temperature, and a few other basics. But the higher level diagnostics are very powerful – read our next blog to learn more.
Combine all of these unique features together, and you’ll understand why company after company keeps switching to trust Draeger sensors for their safety needs!